What is Porosity in Welding: Necessary Tips for Achieving Flawless Welds
Wiki Article
Understanding Porosity in Welding: Discovering Reasons, Results, and Prevention Methods
As experts in the welding market are well aware, understanding the reasons, effects, and avoidance strategies associated to porosity is crucial for achieving durable and reputable welds. By delving right into the origin triggers of porosity, analyzing its damaging impacts on weld high quality, and exploring efficient avoidance approaches, welders can enhance their understanding and skills to produce premium welds regularly.Usual Root Causes Of Porosity
Porosity in welding is mostly created by a combination of elements such as contamination, improper protecting, and inadequate gas coverage throughout the welding process. Contamination, in the form of dust, grease, or rust on the welding surface, develops gas pockets when warmed, causing porosity in the weld. Incorrect securing happens when the shielding gas, generally utilized in processes like MIG and TIG welding, is not able to totally shield the liquified weld swimming pool from reacting with the bordering air, resulting in gas entrapment and subsequent porosity. Additionally, inadequate gas insurance coverage, often because of inaccurate circulation rates or nozzle positioning, can leave parts of the weld unprotected, permitting porosity to form. These aspects jointly add to the formation of spaces within the weld, damaging its integrity and potentially causing structural problems. Understanding and attending to these typical reasons are critical action in preventing porosity and guaranteeing the top quality and stamina of welded joints.Impacts on Weld Quality
The visibility of porosity in a weld can considerably compromise the total quality and integrity of the welded joint. Porosity within a weld creates spaces or cavities that weaken the structure, making it much more at risk to fracturing, rust, and mechanical failure. These gaps work as stress concentrators, reducing the load-bearing capability of the weld and increasing the likelihood of premature failure under applied stress and anxiety. Furthermore, porosity can additionally function as possible websites for hydrogen entrapment, further aggravating the deterioration of the weld's mechanical residential properties.Moreover, porosity can prevent the effectiveness of non-destructive screening (NDT) strategies, making it testing to identify other defects or suspensions within the weld. This can cause significant safety concerns, especially in essential applications where the structural integrity of the welded parts is extremely important.
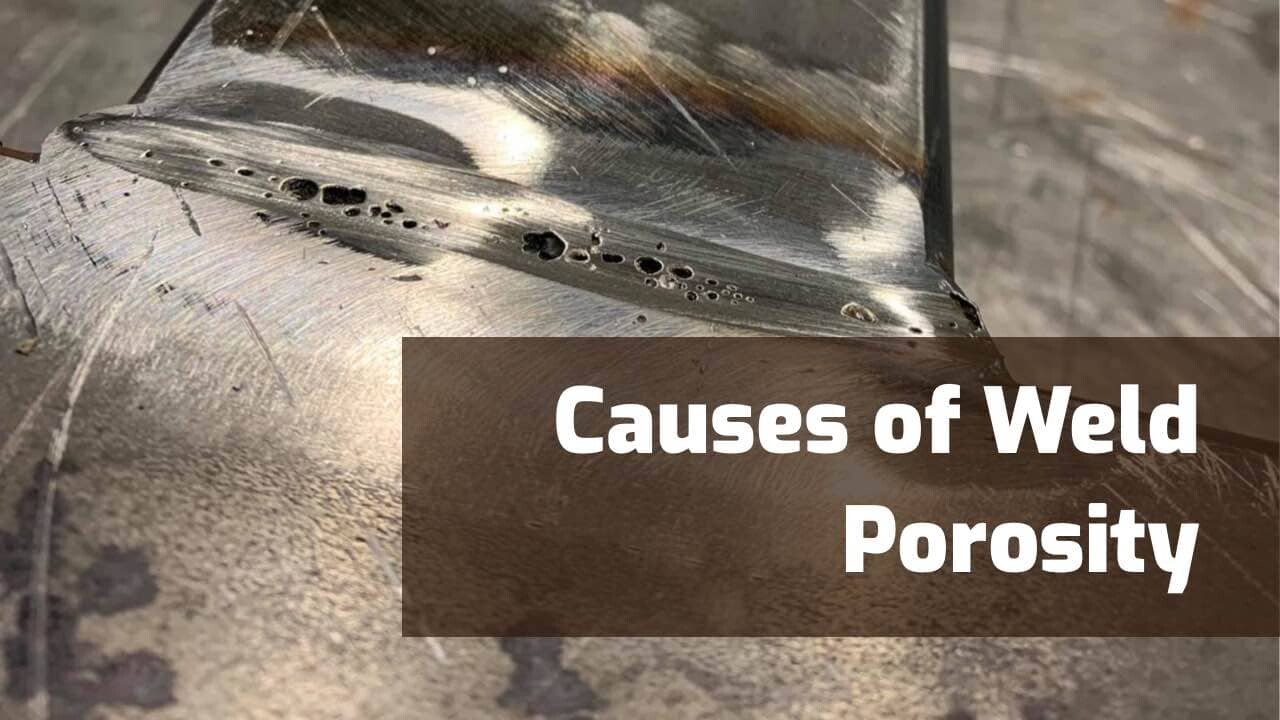
Avoidance Techniques Overview
Given the harmful effect of porosity on weld high quality, reliable avoidance strategies are crucial to maintaining the structural integrity of welded joints. Additionally, choosing the suitable welding criteria, such as voltage, existing, and take a trip rate, can assist lessen the threat of porosity development. By including these avoidance strategies here are the findings right into welding methods, the incident of porosity can be substantially minimized, leading to more powerful and a lot more trusted bonded joints.Relevance of Correct Shielding
Proper shielding in welding plays a vital role in preventing atmospheric contamination and making certain the honesty of welded joints. Shielding gases, such as argon, helium, or a mixture of both, are commonly made use of to shield the weld swimming pool from reacting with elements airborne like oxygen and nitrogen. When these responsive aspects enter call with the warm weld pool, they can cause porosity, leading to weak welds with lowered mechanical residential or commercial properties.
Inadequate protecting can result in different defects like porosity, spatter, and oxidation, endangering the structural stability of the bonded joint. As a result, adhering to appropriate securing practices is important to create high-quality welds with very little issues and make sure the long life and reliability of the welded parts (What is Porosity).
Monitoring and Control Techniques
Exactly how can welders efficiently keep track of view publisher site and manage the welding process to guarantee optimal results and prevent defects like porosity? By continuously monitoring these variables, welders can identify inconsistencies from the excellent problems and make prompt changes to protect against porosity development.
In addition, executing appropriate training programs for welders is necessary for keeping track of and controlling the welding process successfully. What is Porosity. Informing welders on the significance of maintaining consistent parameters, such as correct gas protecting and take a trip rate, can aid prevent porosity problems. Regular assessments and accreditations can additionally guarantee that welders excel in tracking and managing welding processes
In addition, using automated welding systems can enhance tracking and control capabilities. These systems can specifically control welding specifications, decreasing the chance of human mistake and making sure regular weld top quality. By integrating innovative monitoring modern technologies, training programs, and automated systems, welders can successfully check and control the welding procedure to decrease porosity problems and achieve top notch welds.
Conclusion

Report this wiki page